Our TECHNOLOGY
GBM’s scope is making materials recyclable, infinitely. We produce building blocks and objects in a natural way, starting from waste materials and using non-pathogenic bacteria, harmless to humans and the environment. GBM process has four components: waste materials, GBM Bacteria, GBM Nutrients, and water. To make a block of biomaterial, we pour in mold crushed wastes, our GBM Nutrients, and GBM Bacteria: bacteria work for 7 to 28 days (depending on the final hardness wanted) and then the natural block is ready. GBM Bacteria produce a natural adhesive made of calcium carbonate (CaCO3, it is the same material of corals and seashells), that forms a mesh around the crushed particles of waste and keeps them together.

GBM process has four components:
waste materials, GBM Bacteria, GBM Nutrients, and water. To make a block of
biomaterial, we pour in mold crushed wastes, our GBM Nutrients, and GBM
Bacteria: bacteria work for 7 to 28 days (depending on the final hardness
wanted) and then the natural block is ready. GBM Bacteria produce a
natural adhesive made of calcium carbonate (CaCO3, it is the same
material of corals and seashells), that forms a mesh around the crushed
particles of waste and keeps them together.
GBM process is low CO2, as
almost the whole emission from our process is indirect, by upstream production
of GBM Nutrient; low energy, since there is no need for energy expect than
mixing, keeping the bacteria at an ideal temperature (10°C to 30°C) and drying
out (50°C to 70°C) the final product. With GBM, at least 80% of CO2
saving is achieved compared to the production of concrete or wood incineration.
When the Final Product, built with GBM process, comes at the end of its life, it is possible to crush it again and continue recycling, over and over (about 5% of new waste may be necessary for each recycling step).

GBM is applicable to several waste
materials such as excavation, construction, wood, masonry, mine wastes, glass,
paper, TNT (material of the surgical covid-19 masks) and, in future, to plastic
and hazardous wastes (e.g.: wastes enclosing heavy metals). The shape of Final
Products adapts to the mold’s shape: tiles, bricks, pipes, chairs, tables. It
is even possible to build complex structures such as houses made of recycled
wood treated with GBM process.
The strengths that we validated so
far is 30 MPa (construction-grade) for construction waste and 9 MPa (like
bricks) for wood waste. It is also possible to process a mix of different types
of wastes together in the same mold, to obtain various technical performances
(thermal insulation, acoustics, strength).
Our process involves also other
important natural techniques, to obtain a final product:
- Anti-fire powder: an organic flame retardant obtained
by the microencapsulation of chlorine cells that, mixed with wood makes it
anti-fire (the material reacts in presence of combustion)
- Anti-scratch superficial treatment: a treatment with
silica powder that, sprayed over the surface makes it un-scratchable (it is
similar to a glass coating)
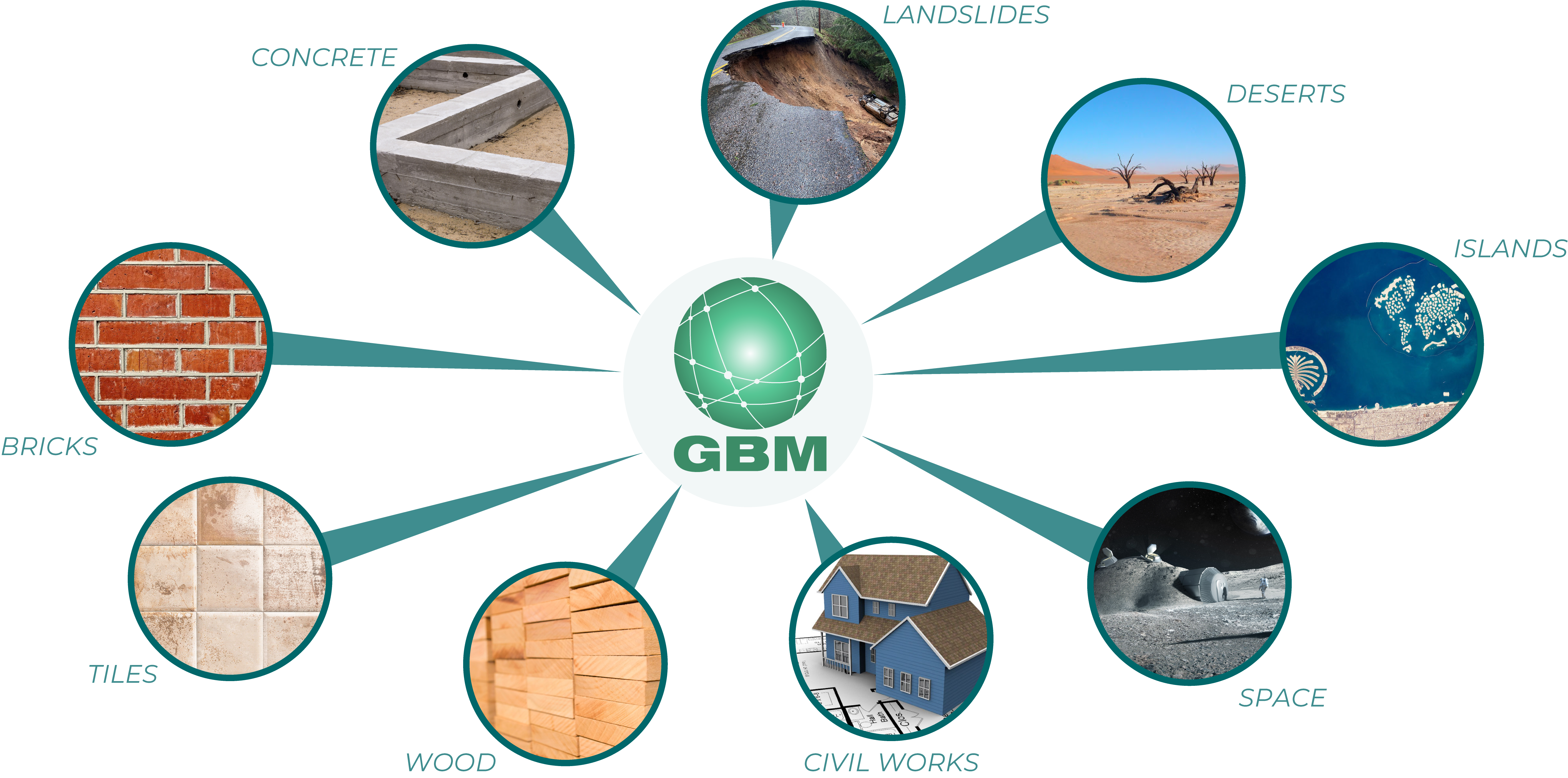
GBM technology can be exploited for many uses, such as ground stabilization around rivers, oceans, desert dunes; building natural foundations for buildings, roads, and railways; reducing heavy metals’ leachability in polluted soil and water; space applications, …
Compressive Strength
Tests conducted on samples made with GBM process, through ASTM C39 on
cylindrical and parallelepipedal (brick) samples.
BASE MATERIAL |
PRODUCTION TIME |
SAMPLE
DIMENSIONS [ cm ] |
PRESSURE STRENGTH
[MPa] |
|||
Height |
Length |
Width |
Diameter |
|||
SAND |
28 days |
15.3 |
- |
- |
7.5 |
30.3 |
SAND |
28 days |
14.4 |
- |
- |
7.4 |
24.7 |
SAND |
28 days |
14.4 |
- |
- |
7.4 |
21.1 |
SAND |
28 days |
15.1 |
- |
- |
7.4 |
22.8 |
WOOD |
14 days |
5.6 |
24.1 |
11 |
- |
7.5 |
MDF (Glued Wood) |
14 days |
5.7 |
23.8 |
10.9 |
- |
9.3 |
CLAY |
14 days |
5.7 |
24.0 |
10.9 |
- |
9.4 |
66% WOOD – 34% CLAY |
14 days |
5.6 |
23.9 |
11 |
- |
5.5 |